Turing, a digital solutions provider, was able to use it’s TOPClear platform for water treatment to apply its PerformSWDesal module to enhance plant efficiency and energy usage at the Gold Coast Desalination Plant in Southeast Queensland, Australia.
The Challenge
The Gold Coast Desalination Plant (GCDP) is a critical infrastructure for Southeast Queensland, designed to ensure water security during periods of drought. While desalination was chosen for its reliability and the abundance of seawater, the process is notably energy-intensive. It requires substantial electricity, typically sourced from energy production methods that contribute to climate change, posing a significant environmental challenge. The plant needed a solution to reduce its energy consumption while maintaining its essential function of providing clean drinking water.
The Solution
To address this challenge, Turing collaborated with the plant and Veolia’s dedicated team to implement TOPClear’s PerformSWDesal module. This module leverages Machine Learning (ML) optimization aimed at enhancing the operational efficiency of the Reverse Osmosis (RO) processes. By analyzing shared operating data from the plant, PerformSWDesal provided recovery set point recommendations for each RO train, optimizing the plant’s energy usage.
The PerformSWDesal standard onboarding process involved three phases:
- Presenting Theoretical Results: Turing’s domain and water experts requested historical operating telemetry data, along with the plant’s operating constraints and procedures. This data was used to instruct the PerformSWDesal machine learning module for each RO train, producing initial optimization results.
- Trialing Set Point Implementation: The effectiveness of the recommended set points was tested by implementing them in a controlled manner. Daily data was shared with Turing’s experts, who used the ML module to generate daily set points for plant operators. Performance tests were conducted to verify real-world energy savings.
- Regular Set Point Operation and Potential Full System Integration: If requested, the optimized set points could be integrated into the plant’s regular operations for continuous energy efficiency improvements.
The Results
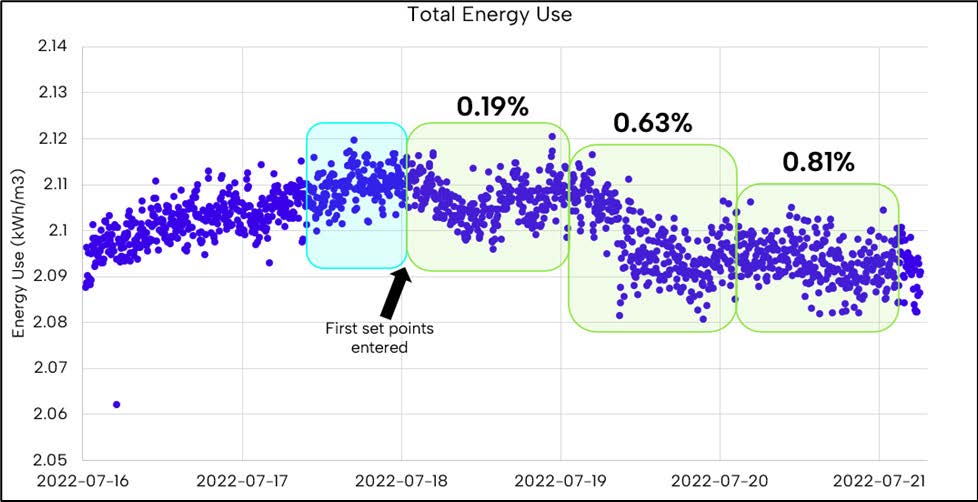
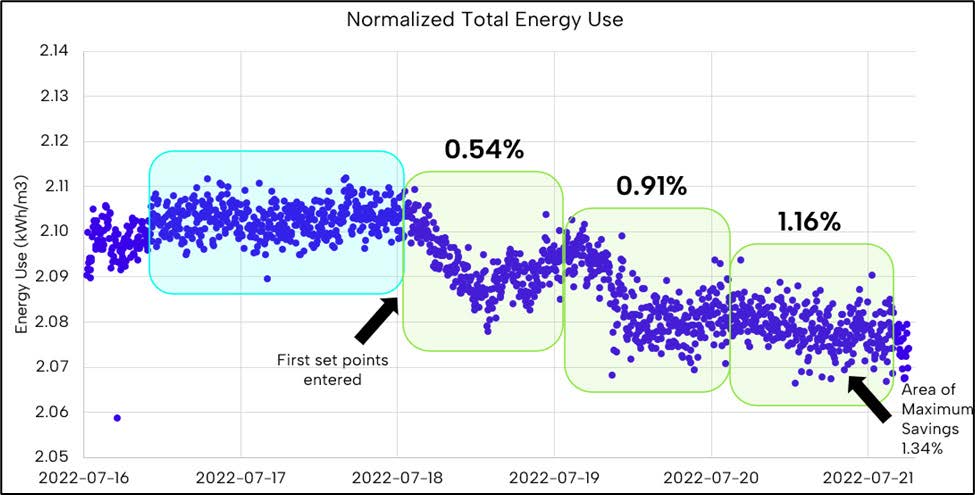
Based on the raw energy use data, shown in Figure 1, the plant energy use dropped following the implementation of the PerformSWDesal set points resulting in an average savings of approximately 0.55% and a maximum decrease of 0.81%. Normalizing the power data to account for the increasing cartridge filter dP resulted in an agreed upon savings percentage of 1.16%, with a maximum savings percentage of 1.34% near the end of the third test day.
Due to the plant’s pressure-center design, the optimization aimed to achieve the lowest combined feed pressure for all trains at the target permeate flow rate. This design includes four high-pressure pumps that generate the required flow and pressure for the nine RO trains via a shared feed manifold. By minimizing unnecessary pressure in this manifold, the high-pressure pumps could operate at a lower pressure, reducing the plant’s overall energy consumption. The individual train recovery was adjusted within an allowable range of 43.5% to 46% to manipulate the required feed pressure effectively.
The Benefits
The implementation of TOPClear’s PerformSWDesal provided several significant benefits:
Energy Savings: Performance testing, conducted in July 2022, demonstrated that the plant’s energy use decreased following the PerformSWDesal set points implementation. The plant achieved an average energy savings of approximately 0.55%, with a maximum savings of 0.81%. After normalizing the data to account for rising differential pressure in the cartridge filters, the agreed-upon savings were 1.16%, with a peak savings of 1.34%.
Operational Efficiency: The PerformSWDesal set points enabled the plant to optimize energy usage without compromising the required permeate flow or exceeding design limits. This optimization ensured stable and efficient plant operations.
Environmental Impact: The energy savings translated to 0.023 kWh/m³ less electricity used, amounting to a reduction of 1044 MWh annually. In the local Gold Coast area, this equates to an estimated reduction of 762 tonnes of CO2 emissions per year, significantly mitigating the plant’s environmental impact.
Potential for Further Optimization: Additional energy savings of 1.0% to 1.5% could be achieved if the plant could individually set permeate flows by train. This potential further underscores the value of PerformSWDesal optimization capabilities.
Successful Implementation: The plant met most criteria for a fair analysis during the performance testing, operating with the same trains and stable feed water conditions throughout the test period. Despite some minor inconsistencies, such as the rising differential pressure of the cartridge filters, the results validated the effectiveness of the PerformSWDesal set points.
Conclusion
The collaboration between Turing and the Gold Coast Desalination Plant demonstrated that Machine Learning optimization could significantly enhance energy efficiency in water treatment processes. The PerformSWDesal module within the TOPClear platform successfully optimized the plant’s operations, resulting in substantial energy savings and a reduction in carbon emissions. Encouraged by these results, the GCDP team decided to continue with phase three, incorporating optimized set points into regular operations for ongoing improvements. This project highlights the potential of advanced technology in addressing environmental challenges and enhancing the sustainability of essential infrastructure.